Galvanizing is a fundamental process for safeguarding metal surfaces from the ravages of corrosion. Corrosion, caused by prolonged exposure to moisture, oxygen, and other environmental elements, can significantly reduce the lifespan and structural integrity of metal products. Galvanizing addresses this issue by applying a protective layer of zinc to the metal surface, which serves as a barrier between the base metal and the environment. This article delves into the various galvanizing methods, the science behind the protection it offers, its applications, and the industries that rely heavily on this essential process. Companies like BonnGulf play a crucial role in providing galvanizing solutions, ensuring metal products remain durable and corrosion-resistant across multiple sectors.
How Galvanizing Works?
At the heart of galvanizing is the principle of cathodic protection. Zinc, a highly reactive metal, is more readily oxidized than iron or steel. By coating steel or iron with zinc, the zinc will react with corrosive elements first, effectively “sacrificing” itself to protect the base metal. This means that even if the zinc layer is damaged, the underlying metal remains safe from rusting because the zinc continues to corrode in place of the metal.
This process is particularly effective because zinc has a unique ability to form a tough, protective patina—comprising zinc oxide, zinc hydroxide, and other compounds—when it reacts with oxygen and moisture in the environment. This patina not only serves as a barrier to further corrosion but also prevents moisture and oxygen from reaching the metal surface.
In addition to cathodic protection, the physical barrier effect provided by the zinc layer prevents the primary causes of corrosion—oxygen and water—from penetrating the surface of the metal. This dual mechanism is why galvanizing has become one of the most reliable methods of protecting metals from the effects of rust and degradation.
Types of Galvanizing
There are several methods of applying zinc to metal surfaces, each suited to different applications and providing varying levels of protection. Below are the main types of galvanizing processes used in modern industries:
1. Galvanic (Electroplating) Method
The galvanic method, also known as zinc electroplating, involves the electrochemical deposition of zinc onto a metal surface. In this process, the metal is submerged in an electrolyte solution containing zinc ions. An electric current is passed through the solution, causing the zinc to be deposited onto the surface of the metal.
– Advantages: This method allows for precise control over the thickness of the zinc layer and is ideal for small, intricate parts. It creates a uniform coating, making it suitable for decorative finishes.
– Applications: Galvanic galvanizing is widely used for components like screws, bolts, nuts, and other fasteners, as well as for decorative purposes in consumer products.
2. Hot-Dip Galvanizing
Hot-dip galvanizing is one of the most common and effective galvanizing methods. In this process, the metal part is submerged in a bath of molten zinc, heated to around 450°C (842°F). The molten zinc bonds with the steel or iron, creating a thick, durable layer of zinc alloy that provides long-term protection against corrosion.
– Advantages: This method offers the greatest protection and is suitable for large, heavy-duty structures. The thickness of the zinc layer formed during hot-dip galvanizing can be substantial, making it resistant to harsh environmental conditions, abrasion, and impact.
– Applications: Hot-dip galvanizing is widely used for outdoor structures like bridges, construction beams, pipelines, guardrails, and poles. It’s also commonly applied to metal roofing, fences, and automotive components.
3. Diffusion Galvanizing
Diffusion galvanizing involves placing the metal object in a sealed container with zinc powder under low pressure (around 0.1 atmospheres) and high temperature. The zinc atoms transition to a gaseous state and bond with the metal surface through diffusion. The rotating container ensures uniform coverage, making this process particularly effective for complex-shaped components.
– Advantages: The diffusion method allows for a precise and consistent zinc coating on intricate or hard-to-reach areas of metal parts. This results in a corrosion-resistant layer that is smooth and even.
– Applications: Diffusion galvanizing is used for precision components in industries like aerospace, electronics, and automotive manufacturing where consistent and uniform protection is critical.
4. Cold Galvanizing
Cold galvanizing, also referred to as zinc-rich painting, is a process where a special zinc-containing paint is applied to the metal surface. The zinc in the paint reacts with oxygen to form zinc oxide, which provides corrosion resistance. This method does not involve heating or dipping the metal in molten zinc, making it more convenient for on-site applications.
– Advantages: Cold galvanizing is a cost-effective and simple process that can be applied to large areas, including areas that are already installed in structures. It provides a quick solution for corrosion protection and is often used for touch-ups on previously galvanized surfaces.
– Applications: Cold galvanizing is typically used for temporary or less-demanding applications. It’s commonly applied to fences, gates, automotive parts, and construction components in need of surface repairs.
5. Thermal Galvanizing
Thermal galvanizing involves the direct metallization of the metal surface by spraying zinc powder onto it at high temperatures. The zinc particles adhere to the surface of the metal at high speed, forming a protective layer that can be as thick as 50 microns.
– Advantages: Thermal galvanizing is highly durable and offers excellent resistance to wear, impact, and environmental degradation. The method is particularly suitable for large, flat surfaces or curved structures.
– Applications: This method is widely used for structural steel in construction, as well as for machinery, bridges, and pipelines that need a tough, corrosion-resistant coating.
Thickness and Duration of Galvanizing
The thickness of the zinc layer depends on the galvanizing method used, the duration of the process, and the temperature at which it is carried out. For example, the thickness of a galvanic coating typically ranges from 6 microns to 12 microns, while hot-dip galvanizing can achieve layer thicknesses of up to 1.5 mm. The thicker the zinc layer, the greater the level of protection against corrosion.
The service life of galvanized metal also depends on the thickness of the zinc coating. In highly corrosive environments, thicker coatings are required for long-term protection. On average, hot-dip galvanized products can last for 25 to 50 years, depending on exposure conditions, while thinner coatings like those from electroplating may need more frequent reapplication or touch-ups.
Protective Mechanisms of Galvanizing
One of the standout features of galvanizing is its self-healing property. If the zinc layer is scratched or damaged, the exposed metal will quickly react with oxygen in the atmosphere to form a new layer of zinc oxide, effectively resealing the protective barrier. This self-healing capability ensures that galvanized metal remains corrosion-resistant for long periods, even under challenging conditions.
In addition, zinc provides galvanic protection to the underlying metal. When zinc and iron are exposed to a corrosive environment, the zinc will corrode first, sacrificing itself to protect the iron. This is because zinc is more reactive than iron in the electrochemical series, meaning it will preferentially oxidize in the presence of water and oxygen. This galvanic action ensures that the structural integrity of the iron or steel is preserved.
Advantages of Galvanizing
The widespread use of galvanizing can be attributed to its numerous advantages, including:
- Extended Lifespan: Depending on the method and environment, galvanizing can extend the life of metal products by decades.
- Corrosion Resistance: Zinc offers excellent protection against moisture, oxidation, and environmental exposure, making galvanized products ideal for outdoor use.
- Self-Healing Properties: Scratches or minor damages to the zinc layer self-heal through oxidation, maintaining long-term protection.
- Durability and Toughness: Galvanized coatings are resistant to impact, abrasion, and wear, making them suitable for high-traffic areas or harsh environments.
- Weldability: Galvanized metal parts can be easily welded without compromising the protective zinc layer.
- Cost-Effective: Galvanizing provides long-lasting protection at a relatively low cost compared to other protective methods like painting or using stainless steel.
- Lightweight: Galvanized products are lighter than their stainless steel counterparts, making them more efficient in terms of handling and transport.
- Adaptability to Various Industries: The ability to apply galvanizing across multiple industries—construction, automotive, marine, and energy—demonstrates its versatility.
Applications of Galvanizing
Galvanizing has a wide range of applications across numerous industries:
– Construction: Structural steel, pipelines, and fasteners are often galvanized to withstand environmental exposure. Metal roofing, fences, and supporting structures are frequently treated with a zinc coating to prevent rust.
– Automotive Industry: Car bodies, chassis, and metal parts are galvanized to protect them from rust, especially in areas prone to moisture exposure. This not only extends the vehicle’s lifespan but also improves safety by maintaining the integrity of critical components.
– Energy Sector: In the power generation and distribution industry, galvanizing protects infrastructure such as transmission line supports, transformers, and pipelines from environmental degradation.
– Shipbuilding: Ships and marine infrastructure are constantly exposed to saltwater, a highly corrosive element. Galvanizing is used to coat ship hulls and other marine components to protect them from saltwater corrosion.
– Household Appliances: Galvanized metal is used in the production of washing machines, refrigerators, and other appliances, providing corrosion protection to extend their operational life.
– Medical Industry: Medical instruments and implants may be galvanized to prevent corrosion and reduce the risk of infection. Galvanized coatings are also used on hospital equipment to ensure durability.
Galvanizing Services in the UAE
In the UAE, galvanizing services are provided by companies like BonnGulf, a reliable supplier of cable products and accessories, including galvanized rods. The harsh desert environment, combined with coastal exposure in many parts of the UAE, makes corrosion protection essential for infrastructure and industrial projects. BonnGulf and similar service providers play a critical role in ensuring that the region’s metal structures remain durable and corrosion-resistant.
Conclusion
Galvanizing is an indispensable process in modern industry, providing a highly effective and economical solution for protecting metals from corrosion. With various methods available, from hot-dip galvanizing to cold galvanizing, this process is tailored to meet the needs of different applications and industries. Whether it’s ensuring the longevity of steel structures, automotive components, or household appliances, galvanizing offers durable, long-lasting protection, ensuring the integrity and reliability of metal products for years to come.
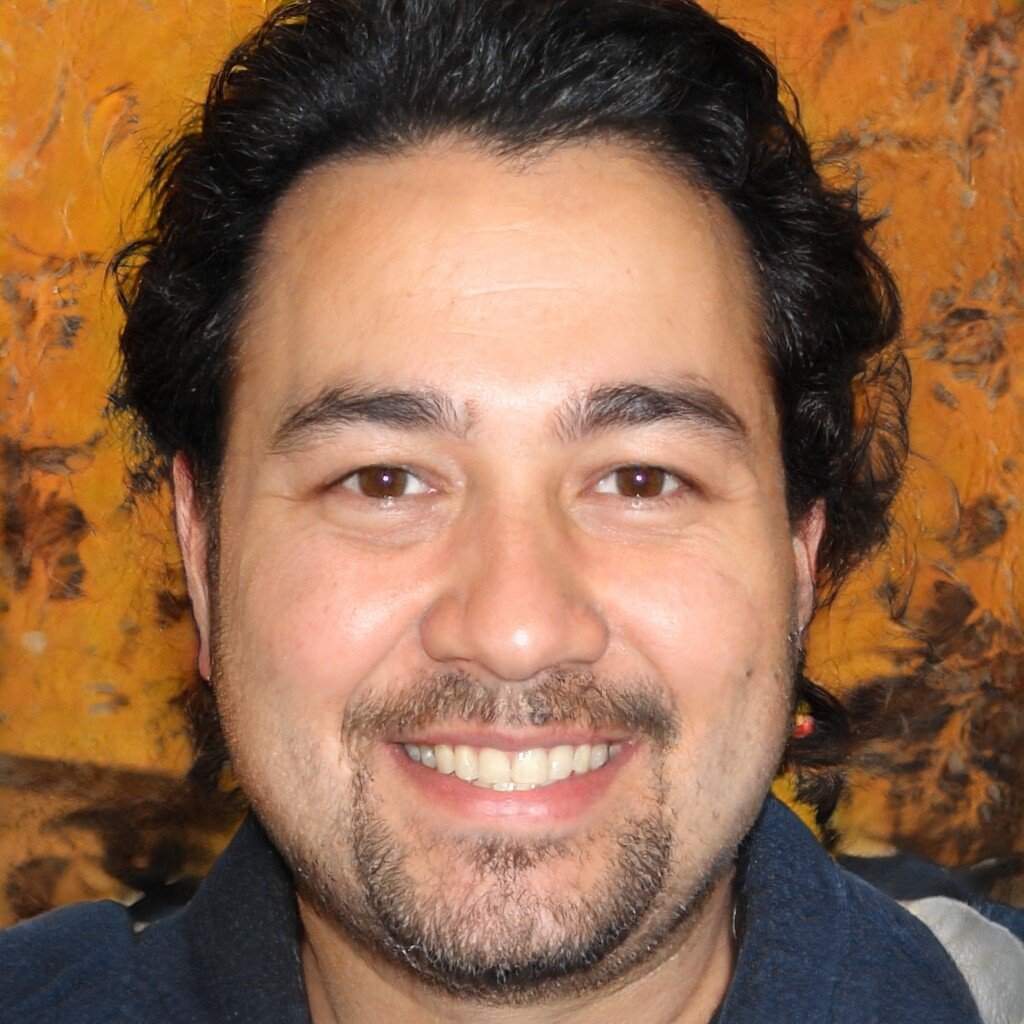
Skier, follower of Christ, guitarist, Saul Bass fan and holistic designer. Producing at the junction of art and sustainability to craft meaningful ideas that endure. I prefer clear logic to decoration.